The Old War Office Project
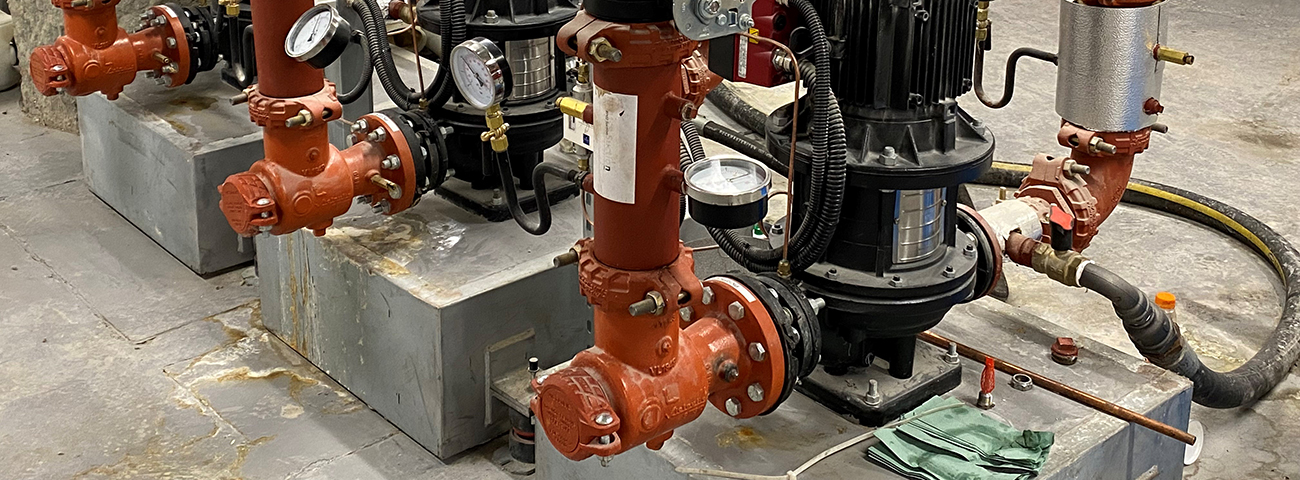
- Accommodating for Angular Deflection
- Accommodating for Movement
- Fabrication
- Carbon Steel
- Accommodate for Thermal Movement
- Compressed Construction Schedule
- Confined Space Installation
- Construction Modularization
- Cost and Schedule Certainty
- Ease of Installation
- Improved Safety
- Minimized Footprint
- Noise & Vibration Attenuation
- On-site Training & Support
- Retrofit
Structural constraints, limited access, and the risk of damage to existing features all serve to hamper the success of any heritage retrofit. These obstacles were acutely present in the luxury conversion of the Grade II* listed Old War Offices, Sir Winston Churchill’s base during World War II, to one of London’s landmark hotels. Planning and preparation were crucial for this project, where many factors concerning the building’s preservation needed to be considered. Engineer, Aecom, and contractor, STRUCKTOR UK LTD, were tasked with the design and installation of the HVAC piping system for this monumental building transformation.
Their primary concern was the lack of adequate blueprints for the existing infrastructure. Without access to detailed drawings of the existing piping system, it became increasingly clear that problems, like potential pipe collisions, could arise during the design and, more importantly, during the installation phase, which could impact both construction efficiency and the project deadline. The second challenge stemmed from the large amount of trench work that needed to be carried out in confined spaces, another area where the team had identified potential installation problems that could have repercussions on the time spent on the job. With these core challenges in mind, the team needed a pipe joining solution that would fit the following criteria: An easier installation process than welding and flanging, which would have been nearly impossible in the trenches, and the adaptability required for any potential surprises onsite, enabling the team to reroute pipe work more efficiently. They turned to Victaulic to deliver such solutions.
The lighter weight, smaller size yet higher integral strength of grooved components compared to welded or flanged systems, make them ideal for projects that are tight on space and time. In addition to increasing installation speed, eliminating the need for hotworks brings greater onsite safety, especially in confined space installations, where the pipe fitters are even more exposed to welding fumes. Installing a mechanical joining system, which provides a union at every joint, also allows for simple field correction of any alignment errors, minimizing schedule disruptions onsite. Moreover, since grooved products are considerably smaller in footprint compared to flanges, pipes can be installed closer to each other.
Time spent on the jobsite is a critical cost and risk factor, leading contractors to prefabricate parts of the piping system offsite as much as possible. Unfortunately, due to the confined spaces, the large number of stairs and the mechanical rooms being in the building’s basements, this was impossible to do for the OWO retrofit. However, Victaulic was still able to offer solutions that helped to save time, space, and reduced risk on site. This was done by supplying modular Vibration Isolation Pump Drops for the mechanical rooms.
These pump drops provide a factory-tested, single-SKU assembly of products and are easy to handle and help to save on installation time. They are value-engineered to isolate and attenuate vibration caused by pumps and other components in the system, reducing excess noise and stress on pipe joints.
Installing pump drops successfully enabled the crew to cut down labour time and realize efficiencies even without a fully prefabricated model. Subsequently, the contractor was able to have the mechanical areas finished well in advance of the deadline, staying ahead of the construction schedule.
Costin Antonescu, Operations Manager at STRUCKTOR UK LTD, concluded “It has definitely been a positive and productive experience working with Victaulic at the OWO. We received continuous support, like training, site visits, and recommendations about prefabricated solutions, throughout the entire duration of the project. Victaulic solutions have been the best option for us at OWO, helping us to increase productivity and lower the execution time and labour costs.”
External Links:
The Old War Office: Modern Piping Solutions to Old Problems, ABC&D Magazine
The Old War Office: Modern Piping Solutions to Old Problems, Modern Building Services