Tank Battery Maintenance Project
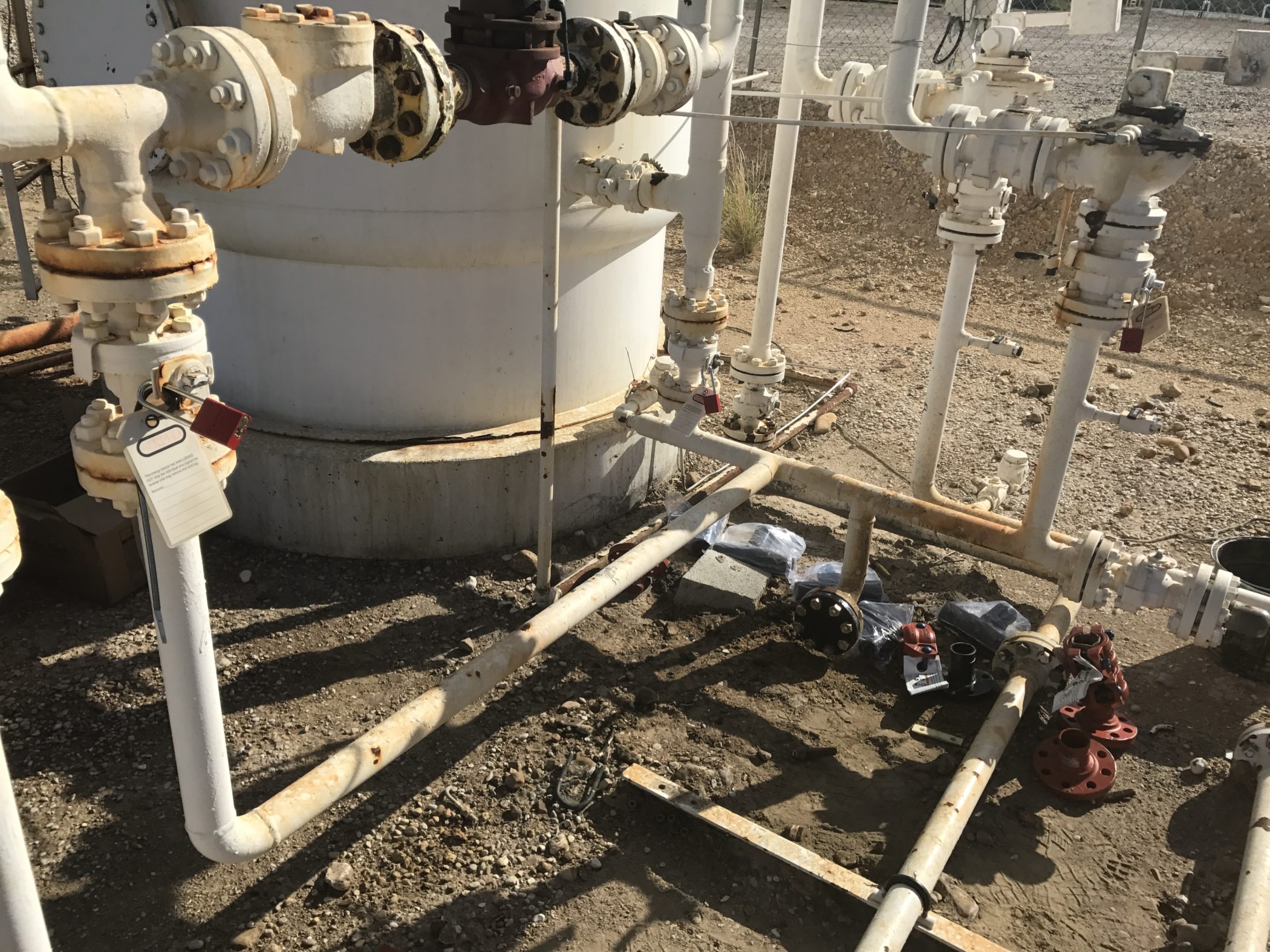
- Virtual Design & Construction
- HDPE
- Compressed Construction Schedule
- Corrosion Resistance
- Ease of Installation
A tank battery in South Texas recently underwent a maintenance program caused by corrosion throughout the pipelines within the facility. The site owner had traditionally used a weld-flange Schedule 80 carbon steel build for their tank batteries, but after seeing the benefits of the Victaulic HDPE system, partnered with Victaulic on this maintenance program.
The facility owner worked with the Victaulic Virtual Design and Construction (VDC) team to configure a drawing package for the tank battery. Having a detailed VDC drawing package allowed for an exact bill of material, mitigating the risk of cost overages or schedule delays.
Once drawings were complete, installation quickly began using Victaulic Style 905 Couplings for HDPE and Style 907 Transition Couplings. The ease of installation enabled the quick and reliable replacement of the corroded pipelines. The maintenance project also included the installation of Series 727 Ball Valves, Style 107N QuickVic™ Rigid Couplings, HDPE fittings, and internally plastic coated (IPC) fittings, mitigating the risk of future corrosion.
By partnering with Victaulic, the facility owner was able to reduce the tank battery maintenance program from three 10-hour days with a six-man crew down to a day and a half of work. The Victaulic system took an average of 2-minutes per joint to install, allowing the owner to bring production back online quickly and reliably, maximizing onsite productivity while reducing the program’s total installed cost.