Nova Aragon Project
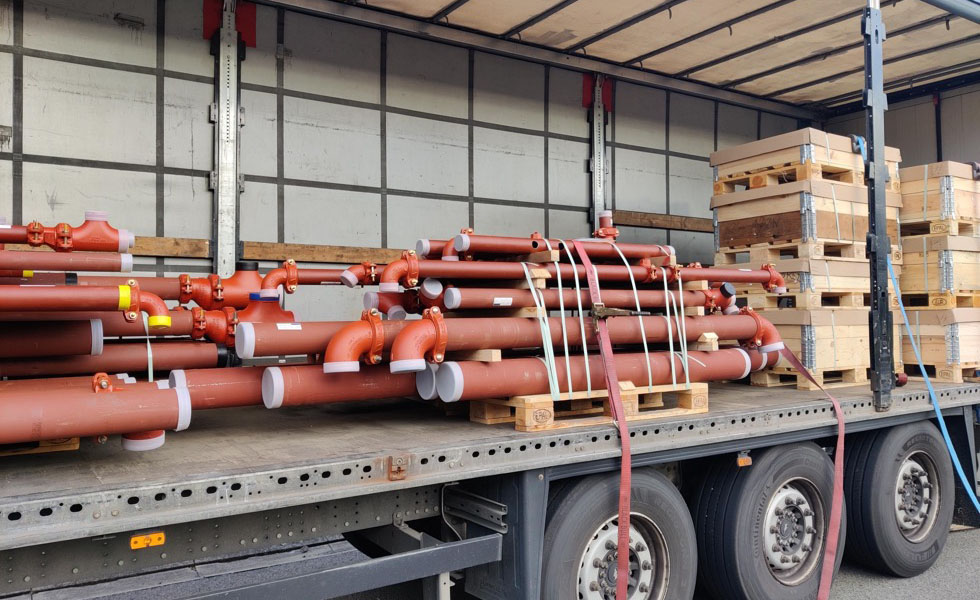
- Accommodating for Movement
- Fabrication
- Project Modeling
- Software
- Training
- Carbon Steel
- Compressed Construction Schedule
- Construction Modularization
- Ease of Installation
The Nova Aragon office project in the Parisian suburb of Villejuif turned to Victaulic’s prefabricated solution to help bring construction in on time. The building’s design was heavily focused on prefabricated elements, being made up of some 950 precast concrete sections and the developer had set a 12-month timeframe for all work to be completed. So, for the HVAC installation, using Victaulic’s grooved pipe joining technology and prefabrication capabilities made perfect sense to ensure work was completed as fast as possible.
As well as using Victaulic’s grooved pipe joining technology, HVAC engineering contractor Proclim CVC also took advantage of Victaulic’s full design, fabrication and delivery services. Victaulic built a dedicated team to manage this side of the project, with representatives from the design, fabrication, logistics and quality divisions.
Proclim CVC specified a rooftop configuration of four reversible chillers feeding 8 Air Handling Units (AHU). These connect to 1,300 fan coils spread over the building’s seven stories. Victaulic’s Virtual Design and Construction (VDC) division designed the optimal piping solution to match this configuration, incorporating more than 1,300 pipe sections and more than 1,000 couplings, as well as 380 elbow fittings, 52 valves and 12 pump drops. The solution covered all piping on the roof including the risers and all connections from the AHUs and chillers.
The VDC team used its in-house Revit® fabrication software, which includes its own bespoke tools built on top of the platform, to complete the work. This is used daily by the company’s global team of around 120 designers and, in addition, the VDC team used BIM modeling to ensure there were no clashes with other aspects of the building’s design. This ensured a truly seamless installation on site.
All sections were cut and finished in the controlled environment of the Victaulic fabrication shop in Nazareth, Belgium to guarantee consistency in quality and also aid faster on-site installation. Delivery was closely coordinated to the required hour and to the precise location that the materials were needed on-site .
This was Proclim CVC’s first project using Victaulic’s prefabricated solution, but the company is already investigating its use in future jobs. Work began at the start of 2020 and was completed by the end of the year. While the overall construction process lasted 12 months, the Victaulic pipe installation was wrapped up inside three months – a timeframe that’s more than twice as fast as a comparable cut-and-weld solution.