Compco Warehouse Project
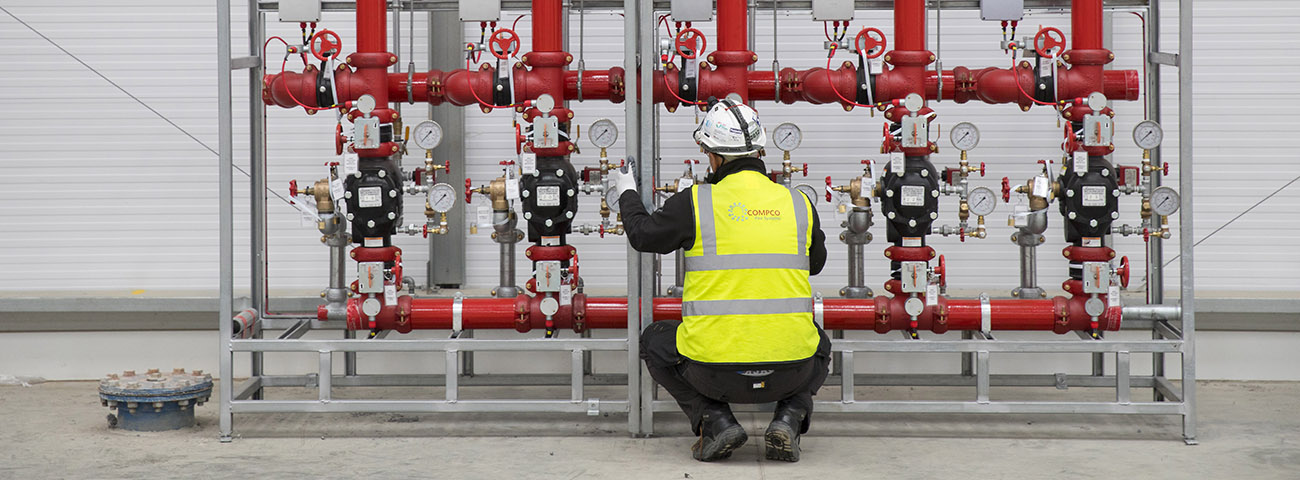
- Fabrication
- Carbon Steel
- Compressed Construction Schedule
- Construction Modularization
- Cost and Schedule Certainty
- Ease of Installation
- Fire Suppression
- On-site Training & Support
- Simplified System Maintenance
Naturally, fire protection is a paramount concern for any property owner. Hopefully the day never comes where the building must be defended against the effects of fire, however, if that unfortunate time does arrive, the future of the property will rest on the carefully constructed protection system put in place. It is not something to overlook, especially for warehouse owners in charge of protecting the company’s stock.
Take for instance B&M’s new distribution centre, which stands as one of the largest warehouses in the UK. The B&M group is the fastest growing variety goods value retailer with stores operating in the UK, Germany, and France. Every installation project faces its own challenges – but when the project is one of the largest in the UK and involves a warehouse measuring 1 million square feet and 22 meters up to the apex, the challenges inevitably become amplified.
In the construction industry, standard practice typically involves the delivery of products at the start of a project to be assembled onsite. This can create significant and unnecessary challenges: time is often wasted, and mistakes are made as contractors search for pieces and try to prepare the correct volume of material for the specified work zone. However, this is not the only option: contractors can instead opt for prefabrication (pre-modulization), where pieces are prepared and preassembled in the required quantities off-site. For this project, which had a limited timeline for completion, Compco Fire Systems (CFS) – the UK’s largest national fire engineering provider – opted to prefabricate much of the fire-proof system – with special attention to the alarm valve modules. This method allows products to be delivered when they are needed rather than in one go, which was essential for B&M’s warehouse installation as there were close to 72,000 rack heads and 54 valve sets involved.
The B&M warehouse is a significant installation challenge – one that relies upon strong communication, well-chosen products, and efficiency. CFS understood that the quality and reliability of its long-time partner Victaulic would be vital. The effective collaboration and prefabrication strategy, combined with regular training and support from Victaulic, ensured much-needed efficiency that is spearheading a successful installation.
Commenting on the B&M installation, CFS Construction Manager, Kevin Jinks, said: “The B&M installation was one of the largest projects of its type in the UK. We therefore needed an installation partner we could rely on and with 18 years’ experience working with Victaulic, they were an obvious partner. The maintenance engineers we work with are always familiar with Victaulic products and know exactly what they are getting. They enjoy the ease of Victaulic’s interchangeable solution: it’s the simplicity of the product which is the real bonus. As well as providing high quality and reliable solution to an installation of this scale, Victaulic provided comprehensive onsite training across all elements of the installation process. The effective collaboration between Victaulic and the onsite engineers meant that significant time-installation savings were achieved, and products were fitted correctly and consistently.”