Canoe Creek Hydro
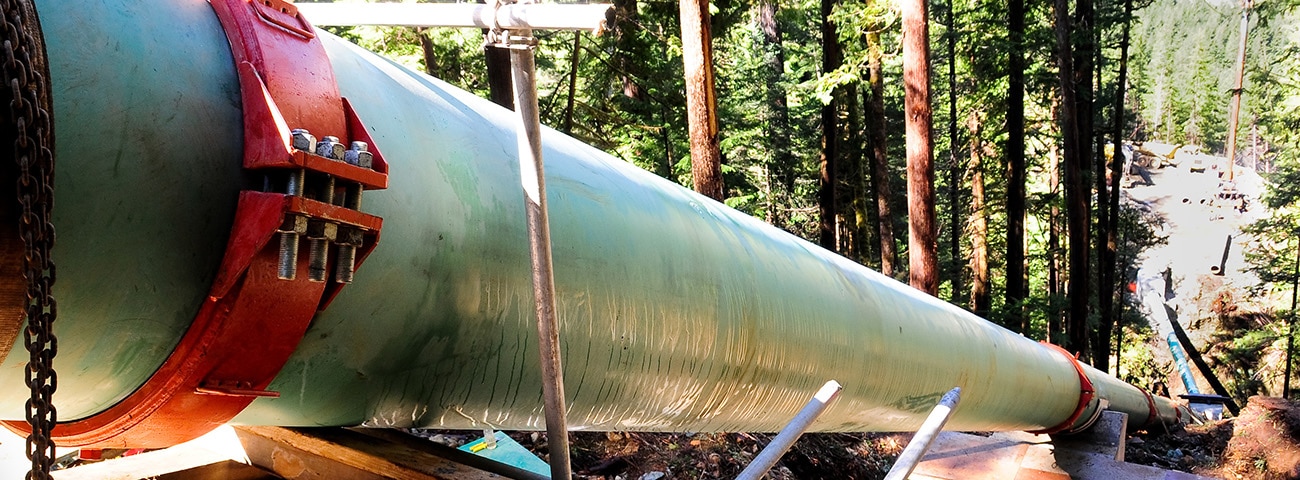
- Carbon Steel
Canoe Creek is a 5.5-megawatt run-of-river hydroelectric facility built to aid Vancouver Island in becoming more energy self-sufficient. To divert stream flow downhill to the powerhouse, a four-kilometer, 36”/900mm diameter penstock piping line was constructed. Located in the Pacific Rim Rainforest, where annual precipitation is amongst the heaviest in the world, a challenging installation took place where the terrain is as steep as an 84 percent grade. In such harsh conditions, traditional methods of welding for the penstock would have been challenging, and staying on schedule would have been next to impossible.
To address these issues, the owner of Barkley Project Group and Hazelwood Construction, the contractor, decided to install 36” Victaulic AGS Couplings on the penstock. During construction, rain often fell heavily, but since Victaulic couplings could be installed in any weather condition, crews were able to proceed without costly delays.
This installation of this penstock line had a significant environmental impact. Tree removal needed to occur in order for the penstock line to be constructed. A road/path was cleared to allow crews to build the line. The use of Victaulic’s grooved couplings eliminated the need for large equipment, such as vehicles and tents, required for welding. This resulted in a reduction of the road size which reduced deforestation. Originally, the road was supposed to be 18 km wide. Because Victaulic’s Grooved Couplings were utilized, the road only needed to be 6 km wide.
In addition to the minimized construction footprint, another environmental benefit of the project was the reduced emissions and fuel consumption. Welding the 154 pipe joints would have produced about 37,422 kg of CO2 emissions using a diesel-powered welding machine and 8,779 kg of CO2 using an electric machine. Grooving and coupling that same run of pipe would produce about 58 kg of CO2.
Victaulic proved to be the perfect solution resulting in the early completion of the project. A pipe joint that typically would have taken up to six hours to weld was completed in less than 20 minutes. The two-piece housing design of the Victaulic couplings allowed fast and easy installation which could be visually inspected. Specialized personnel and x-ray joints typically required to weld were not required.
Victaulic also improved site safety as the pipe could be grooved and re-coated on-site prior to sending it up the single-lane logging road to be assembled. This process eliminated the need for field repair and repainting of the line post assembly, allowing for less noxious fumes and fewer delays.
The use of mechanical couplings rather than more traditional welded joints when installing the penstock at the 5.5-MW Canoe Creek facility saved time and money and provided a safer environment and for the workers.
External Links
Mechanical Couplings Replace Welding at Canoe Creek, Hydro Review
Grooved advantage in the field, Water Power & DAM CONSTRUCTION