Posted on April 3, 2020
For centuries, the United States has relied on hydropower dams and plants to provide clean, cost-effective and renewable energy. As the demand for hydropower energy sources continues to grow, many of the aging hydropower plants must undergo renovations to meet the needs of today’s society. Renovations and enhancements to powerplants can be expensive, time-consuming, and potentially dangerous. Victaulic is able to provide solutions that help hydropower plants powering the nation.
History
For centuries, people have utilized the force of flowing water, from streams and rivers, to produce energy. The concept of using flowing water to generate electricity was first introduced in 1813 by Michael Faraday, an English physicist, and chemist. Faraday discovered that electricity could be created by using a magnet and a copper wire. Faraday used the force that he found in the magnetic field of a magnet to pull the copper’s electrons out of their orbit to create electricity.
While this was an important discovery, it was not until the 1870s and 1880s when Faraday’s findings became more relevant in society. At the time of Faraday’s invention, there was little need for a generator because the commercial technologies that relied on electricity, such as lights, had not been invented yet. In September 1882, when Thomas Edison opened his Pearl Street Station in New York City, the commercial value of electricity was established. Edison’s complete electrical circuit that generated power at a central plant and carried it by copper wires to buildings in the surrounding district was powered by steam. The problem with Edison’s discovery was that the electricity had a limited distance that it could travel. The direct current (DC), that powered Edison’s incandescent bulb could only travel one-half miles from his Pearl Street Station.
Quickly realizing this limitation, H. J. Rodgers, a businessman from Wisconsin, connected Edison’s electrical circuit to a waterwheel on the Fox River. The power of the running water from the Fox River allowed Rodgers to produce enough electricity to light his home and two nearby paper mills. By 1886, approximately 50 hydropower plants were online or under construction in the United States and Canada. These hydropower plants were taking advantage of nearby water sources to generate electricity and distribute it to the local communities. Unfortunately, there was still a challenge of finding a way to transport electricity across miles to outlying areas and places without a ready water source.
In 1896, Nikola Tesla harnessed the power of Niagara Falls to transmit electric power, across the distance of 26 miles, to Buffalo, New York. This high-voltage alternating current (AC) was championed by Nikola Tesla and George Westinghouse, manufacturing giant. The advancement of AC power allowed electricity to be produced less expensively and able to be transmitted over longer distances. By 1902, AC power plants, powered by Niagara Falls, were producing one-fifth of all electricity generated in the United States.
Faraday Dam and Powerhouse
Throughout the early 1900s, many additional hydropower plants were built, especially on the West Coast. As the population on the West Coast began to rise, so did the need for electricity. In 1904, construction began on the Faraday Hydropower Plant by Oregon Water & Power Company (OWP). The plant was completed in 1907 after OWP became a part of the Portland Railway Light and Power in 1906. (The company later became Portland General Electric in 1930.)
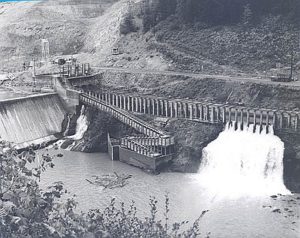
The Faraday Dam and Power House was the second largest hydroelectric plant constructed in the Portland region. Located on the Clackamas River in Estacada, Oregon, the hydropower plant was designed to produce hydroelectricity to serve the greater Portland area. This hydroelectric development allowed for the expansion of the Portland-area industry, as it provided the needed power for manufacturing and lighting.
The hydropower plant was designed to create power through water that was diverted from the main channel of the Clackamas River by the Cazadero Dam, built 1.5 miles upstream from the powerhouse to Faraday Lake. The water then drops almost 180 feet through a series of eight-foot-diameter steel penstocks to the powerhouse where it powers the turbines before returning to the main river channel.
Since 1907, Faraday has provided hydropower to the greater Portland area. By 1956, there was an increased demand for electrical power; to accommodate this demand, the Faraday Powerhouse was expanded to add a sixth-generation unit.
Hydro Continuing to Power Today’s Society
One of the most significant challenges that the United States, and other nations, continue to face is ensuring the availability of low-carbon, affordable, and secure energy. Hydropower has been and continues to be a substantial contributor towards meeting this need. In today’s society, hydropower plants have seen steadily increased growth, which is primarily driven by the demand for reliable, clean, and affordable energy.
Despite the increased demand, the hydropower industry still faces challenges. Availability factors have decreased in the last decade. This presents a challenge to new hydropower development, increases the operations and maintenance costs of aging infrastructure, and requires plants to be operated in new and different ways.
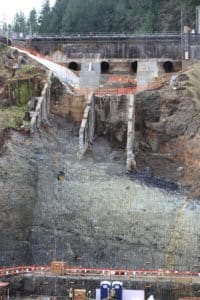
To address these challenges, there have been substantial pushes to retrofit and upgrade aging hydropower facilities over the past decade. In many instances, building new hydropower facilities is cost-prohibitive; it is more feasible to upgrade and retrofit old facilities.
Unfortunately, in many of the old facilities, such as Faraday, there are limited resources, such as drawings, dimensions, facility details, from the original construction and design of the facility. In these instances, despite the limited resources, Victaulic can provide products and solutions to hydropower plants.
“Victaulic can replace existing piping systems inside aging powerhouses with limited detail plans,” explains Zack Almont. A Power Specialist for Victaulic, Almont describes how Victaulic’s solutions allow for field routing and installations inside powerhouses. “Instead of welding in a powerhouse, and facing dangerous conditions such as ventilation and flammables, Victaulic’s grooved piping products provide the flexibility to do retrofits in an efficient and cost-saving way. Contractors can replace entire existing piping systems by using Victaulic’s grooved solutions while saving valuable time and money during the hydropower plant outages.”
Similar to many other hydropower plants in the Pacific Northwest, the Faraday Powerhouse is currently undergoing a major repower, that started in 2019. While several elements of the original building and history will be preserved, the new and more efficient powerhouse is set to open in 2021.
As hydropower plants, such as Faraday, continue to be updated, Victaulic can provide solutions for many of the essential operations. Victaulic’s products and services can support the development and enhancement of penstocks, cooling water and oil-water separators, lube oil, control air, drains, service water, sump, generator suppression, intake controls, and fire protection systems.
Click here to learn more specific information on how Victaulic supports the infrastructure market.