PosLX Saltwater Lithium Project
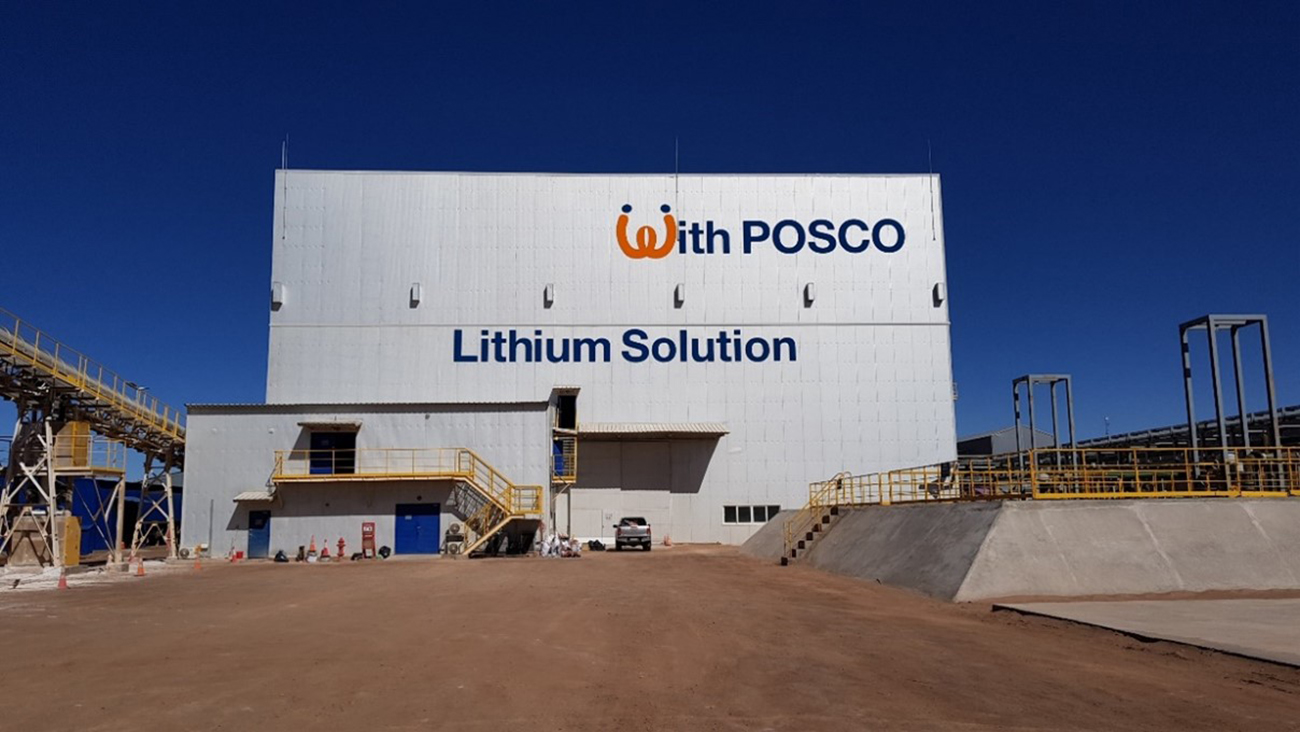
- Training
- Carbon Steel - Galvanized
- HDPE
- Stainless Steel
- Compressed Construction Schedule
- Ease of Installation
- On-site Training & Support
- Reliability
With the recent global surge in demand for electric vehicles, battery companies worldwide are ramping up lithium mining and lithium battery production efforts.
POSCO, a South Korean steel-making giant formerly known as Pohang Iron and Steel Company, has embarked on constructing a lithium commercialization plant in Argentina in 2022. POSCO is currently conducting investment evaluations and research and development on the commercialization of oil-field brine lithium projects through a brine lithium business in Argentina. It has been developing its own DLE technology for the past 6 years and is promoting full-scale commercialization.
This move aims to bolster its lithium capabilities for electric vehicle manufacturing in South Korea. The PosLX investment totals approximately $1.09 billion, split into two stages. The first stage of construction targets completion by the first half of 2024, with a planned annual production capacity of 25,000 tons of lithium hydroxide.
The construction project is confronted with a multitude of challenges. These include extreme weather conditions, such as bitterly cold winters and scorching summers. The project site is located at Salar del Hombre Muerto, 4,000 meters above sea level. The high altitude results in reduced oxygen levels, affecting labor productivity and causing other consequences. To address these issues and expedite construction and production, Victaulic was selected by POSCO to provide a grooved pipe joining method across a range of services and pipe materials ranging from 2” to 12”. This solution includes QuickVic™ Style 107 and QuickVic™ Style 177 couplings, Style 489 Stainless Steel couplings, and Style 905 couplings for HDPE.
The grooved pipe joint offers a solution that requires only semi-skilled labor instead of highly qualified and certified welders, thus streamlining the installation process. Style 489 Stainless Steel couplings were used in the main water and demineralized water systems. Utilizing Installation-Ready™ Technology, the Style 107 & 177 couplings expedite the installation process for fire protection and instrument air systems significantly.
The Victaulic solution for HDPE pipe offers a safe, fast, and weather-independent mechanical joining alternative. This ensures correct installation through visual verification of each coupling. Designed to thrive in adverse and extreme conditions, it guarantees performance that meets or exceeds the pressure ratings of HDPE pipe. Specifically designed for plain end HDPE pipe, over 600 Style 905 couplings were utilized on the Brine lines. These couplings not only facilitate efficient installation but can also be easily disassembled and reinstalled as necessary, offering significant advantages for future project expansions. In contrast, traditional butt-welding methods for HDPE pipes are heavily weather-dependent. This often renders construction impossible during rainfall, highlighting the superiority and convenience of the Victaulic solution.
To ensure construction quality and assist workers who are unfamiliar with the grooved piping joining method of Victaulic, comprehensive on-site training was provided by Victaulic. This training covered grooved Technology, operating principles of Grooved Couplings, material solutions in Stainless Steel, Ductile Iron, and HDPE, as well as setup and operational guidelines for the VE271FSD Roll Grooving Tool.
The success of this project hinges on the collaborative efforts of Victaulic colleagues from South Korea and Argentina. With construction currently underway and expected completion in the first half of 2024, the project aims to achieve installation five times faster and reduce construction costs by over 30%, enabling the project to stay on schedule.