Danderyd Hospital Project
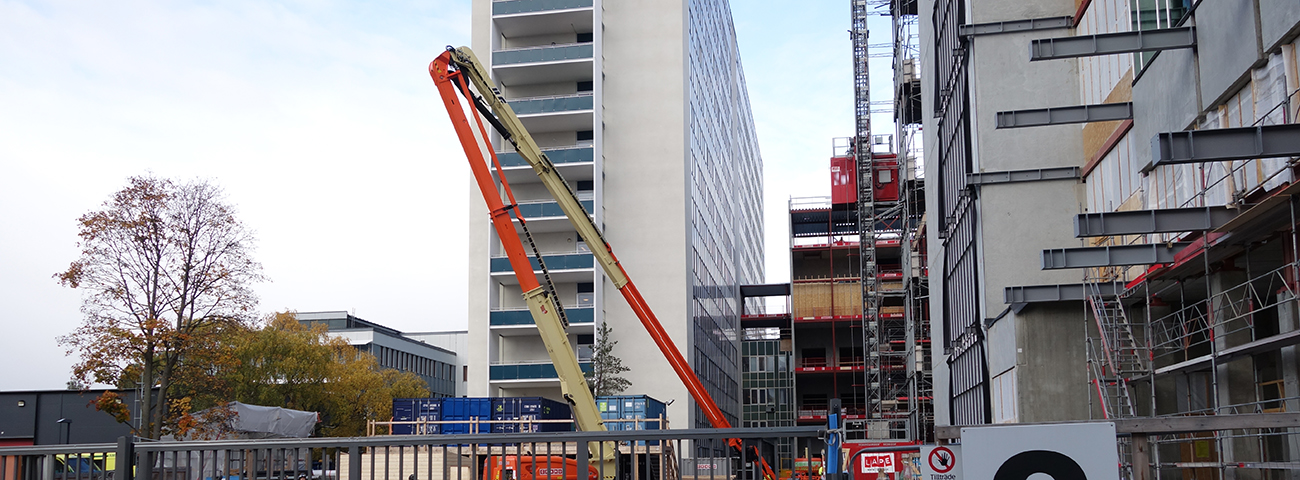
- Fabrication
- Virtual Design & Construction
- Carbon Steel
- Stainless Steel
- Compressed Construction Schedule
- Confined Space Installation
- Cost and Schedule Certainty
- Ease of Installation
- Improved Safety
Tight deadlines, space limitations, stringent hygiene requirements and safe and clean work environments, these are just a few of the many challenges contractors must overcome when working in the healthcare sector. When the Danderyd Hospital put out a tender for an expansion and the installation of a new mechanical room, contractor Sandbäckens Rör knew traditional pipe joining methods were not up to the challenge.
A firm foundation of the project was laid when they decided to partner with Victaulic, who’s grooved couplings and fittings were simply a better fit for the task. Sandbäckens Rör came in with a fixed price for the entire project, which made a sound economy of the utmost importance. Installing a grooved system made installation easier and faster, and workflow more predictable. It also eliminated uncertainties associated with hot works and the amount of man hours on the site. The fact that welding skills are not needed provided greater flexibility and freedom during the installation process and made estimating easier. This also meant that construction workers and the hospital’s staff and patients did not have to worry about the hazards associated with welding, like fire and fumes.
“In addition to the advantages a mechanical piping system brings, Victaulic also contributed with a service package, including project planning and support. This made our work as easy as possible.”, said Ralf Lundqvist, who oversaw the project for Sandbäckens Rör.
What they found particularly useful was the fact that the initial plan drawing was converted into a 3D model by Victaulic. These drawings portray the different zones of the project as they are meant to be built, and include all components, pipe lengths and material lists. These drawings also helped to ensure there were no collisions with existing installations and that the limited available space was optimally used.
Once the 3D model was approved, pipes were cut and grooved in the appropriate lengths, and spools were produced and preassembled in the quantities required, ready for installation on site. For the Danderyd project, approximately 70 percent of the assembly work was carried out offsite, resulting in minimal disruptions in the operational hospital. All fabricated spools had ID-tags and a color code, that were also reflected on the 3D drawings for each zone.
“With grooved pipes, the work is tidy and clean. Victaulic had planned and precisely drawn up blueprints to make everything fit. The 3D drawings are easily comprehendible, and everything is delivered according to the construction schedule and accompanied with the 3D drawing and a plan sheet. It is a system that provides a good overview, and it cannot be easier than this. It is like building with Lego®, adds Magnus Danielson, who headed the assembly work.
The expansion of the Danderyd Hospital started in 2016 and lasted until 2019 and was part of a major hospital modernization project in Sweden. At its most intense phase, Sandbäckens Rör had 30 people working on site. “Everything has proceeded according to plan and is working as expected”, concludes Ralf Lundqvist, “Using a grooved system made this a very financially beneficial project. We surely will use mechanical pipe joining again in the future.”
External Links:
PSBJ July 2018, Public Sector Build Journal
Fast and Clean Pipe Assembly at Danderyd Hospital, Slussen.biz