LEARN HOW THESE GLOBAL PROJECTS HAVE BENEFITTED FROM OUR INSTALLATIONS
Controlling costs and compressing schedules without sacrificing quality are key concerns for contractors responsible for mechanical room installations. Clients are looking for on-time, on-budget delivery of high-quality systems that work well and are easy to maintain. Alongside these drivers, space is becoming a critical factor.
The high cost of commercial and industrial building space and its scarcity has led to a growing trend to squeeze the size of mechanical rooms. Ever tighter architectural designs for new builds are putting pressure on consulting engineers and contractors to deliver reliable, cost-effective HVAC solutions that keep the mechanical room footprint to a minimum. Similar demands are being made for mechanical room retrofits within the structural constraints of older buildings.
Grooved-end mechanical piping systems address all these issues. The lighter weight, smaller size yet higher integral strength of grooved components compared with welded or flanged systems, make them ideal for projects that are tight on space or where mechanical rooms are located on higher-level floors. Their ease and speed of installation offer savings on total installed costs and they also deliver improved performance and reliability.
Switching from welded and flanged specifications to the grooved method for mechanical room installations can make a big difference to the success of a project. Engineers, contractors and owners all stand to gain from grooved systems. Design engineers can realize space savings; contractors can make time and cost savings to achieve on-time, on-budget hand-over to the client; owners get an efficient, reliable system which is easy to maintain.
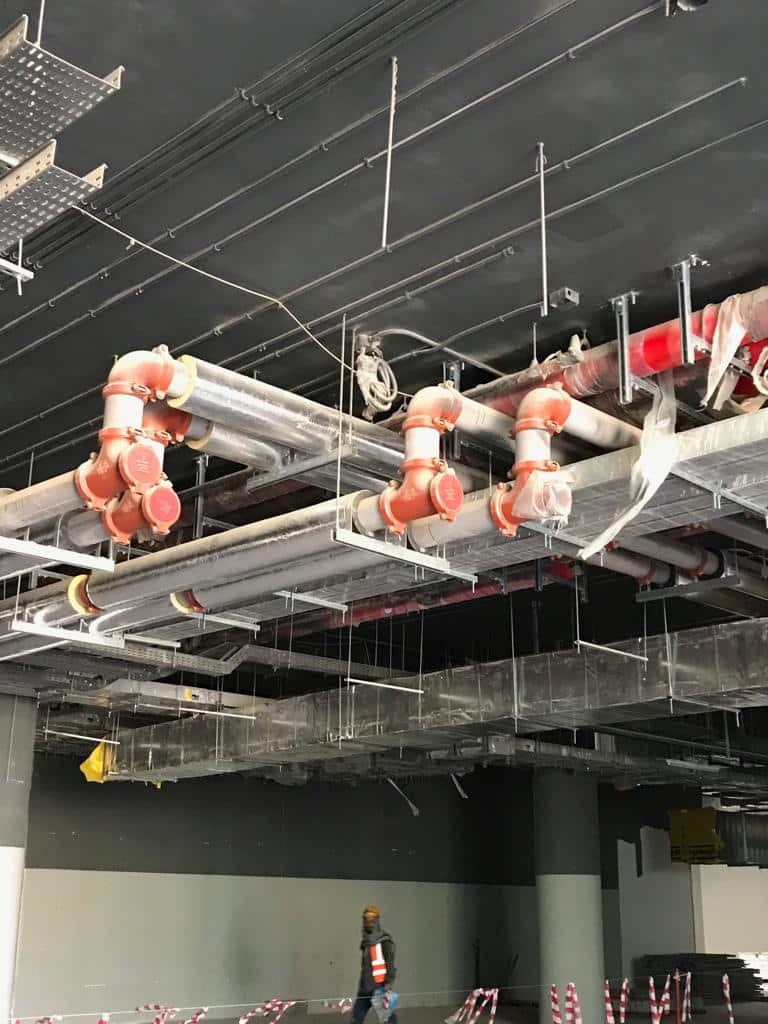
Riyadh Metro, Saudi Arabia
Riyadh Metro, Saudi Arabia saved an estimated 30% on time and cost of mechanical rooms installation as compared to what would have been spent on welding using Victaulic grooved technology.
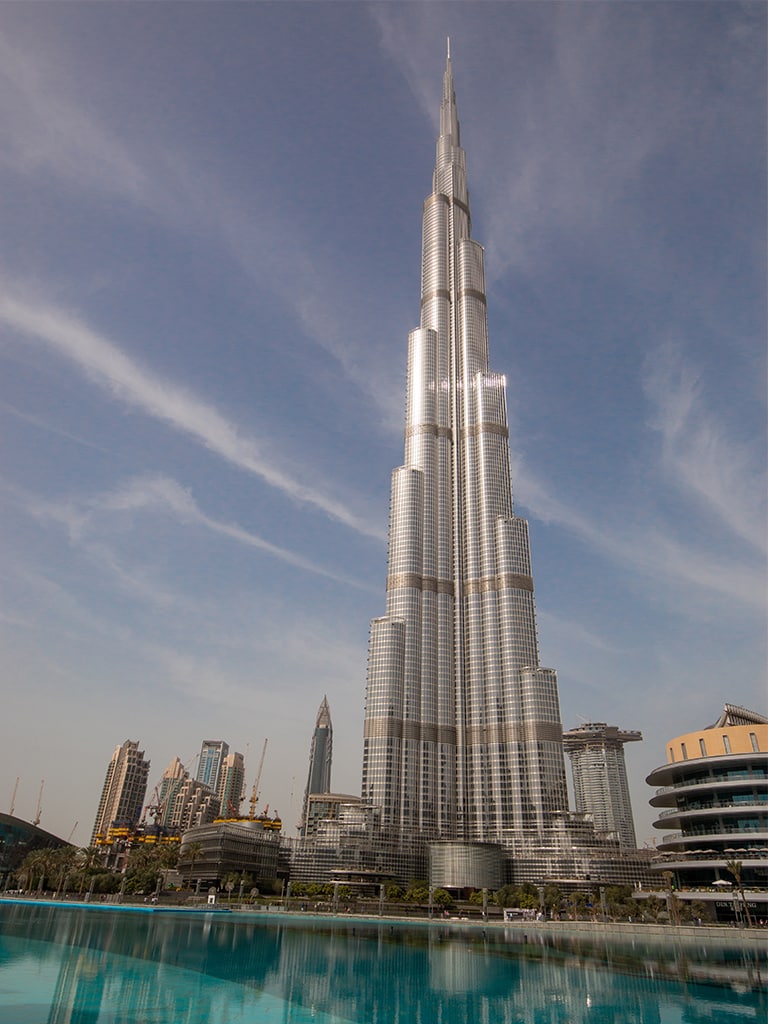
Burj Khalifa, Dubai, UAE
Switching from traditional joining methods to Victaulic mechanical pipe joining solutions in the world’s tallest building, as well as the “dancing” fountain, helped the engineer to meet the design challenges and the contractor to meet the project deadline, while achieving time, cost and labor savings.
UNITED ARAB EMIRATES
Burj Al Arab Hotel
LEARN MORE
CHINA
Shanghai Financial Trade Center
LEARN MORE
SINGAPORE
Esplanade Theatre
LEARN MORE
MALAYSIA
Petronas Towers
LEARN MORE
CANADA
Shell Oil Sands
LEARN MORE
UNITED STATES
Hoover Dam
LEARN MORE
EGYPT
Alexandria Library
LEARN MORE
FRANCE
La Grande Arche de la Défense
LEARN MORE
WANT TO KNOW HOW VICTAULIC CAN BENEFIT YOUR NEXT PROJECT?
TO REQUEST MORE INFORMATION PLEASE FILL OUT THE FORM OR EMAIL [email protected].
VICTAULIC (ALTERNATE CONTACT)
EMEAI HQ: PRIJKELSTRAAT 36 NAZARETH BELGIUM B9810
MIDDLE EAST OFFICE: FZ LIU10 AA01, AA02, AA03, AA04 AND AA05 AL
MUNAWALA ST JEBEL ALI, DUBAI
EMAIL [email protected]
CONNECT WITH THE MIDDLE EAST TEAM ON
WHATSAPP FOR BUSINESS